Manori Wijesekera Mack
The Decade of Productivity launched last year by President Chandrika Bandaranaike Kumaratunga brought into focus the urgent need for a positive change in the standard of productivity in the country. Currently, Sri Lanka continues to lag behind most South Asian countries, her levels of productivity only showing a few shining examples — the exceptions to the rule, rather than exemplary of the whole.
Productivity can be broadly de- fined as efficiency in industrial production, or more specifically as the level of output obtained in relation to the resources utilized. Management gurus have been theorizing on the most effective ways of achieving this remarkable feat of output outgunning input, however, it appears that while these ‘productivity’ principles are helpful, the magie formula is unique to each company.
Local statistics, for the first quarter of 1996, show that the number of work hours per week were highest in the Trade and Hotels industries (50 hrs and over), while most of the other major industrial groups listed averaged 40-49 hrs per week. In a country filled to overflowing with public holidays (23 days in all in 1997), is it possible to achieve and
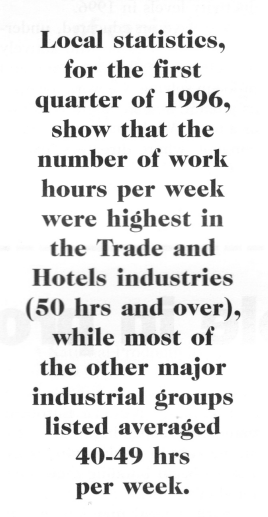
maintain international standards of productivity? ‘Public holidays are here to stay. Once given it’s almost impossible to take it back, and besides many of our local holidays have a religious and cultural context and they are important because they are all part of our culture,’ said II B Masinghe, director/investment, Board of Investment of Sri Lanka. ‘In a multi-religious, multi-ethnic nation like ours, it is to be expected that we end up with so many holidays. However, this need not affect our productivity, From the industrial sector to banking to the agricultural sector, it is possible to make up for whatever disadvantages are brought on by the excess number of holidays. It need not be an obstacle,’ said an executive from a leading merchant bank in Colombo.
‘I think Sri Lanka has fared rather well. We have greatly improved our infrastructure, from telecommunications to shipping. We are drawing in foreign investors who appreciate the advantages of a skilled labor force and the tax incentives offered by the government,’ said Masinghe. ‘I think levels of productivity vary in each industry, and there is definitely room for improvement. But we have a head start on most South Asian competitors because the labor force is literate and quick to learn new skills and technologies.’ Ceylon Tobacco Company Limited (CTC) was the winner of the 1996 National Productivity Award, awarded by the Ministry of Industrial Development. The award recognized the remarkable growth achieved by CTC, following a wave of restructuring and refocusing five years before. They introduced a plethora of ‘firsts’, previously unheard of in the tobacco industry. Open dialogue with trade unions led to the signing of agreements, which enabled the smooth functioning of the ‘team work’ concept. Employees were offered an attractive voluntary separation scheme, and were also advised on investment opportunities and options. Improved work parities were extended to tobacco growers as well, with the company encouraging the farmer to earn more by reducing input costs while increasing their yields and quality of produce. Productivity linked compensation, comprehensive training, effective internal communication with small group meetings and briefings held regularly, all became part of the new strategy of CTC. And their mission gained a clear focus, ‘achieving
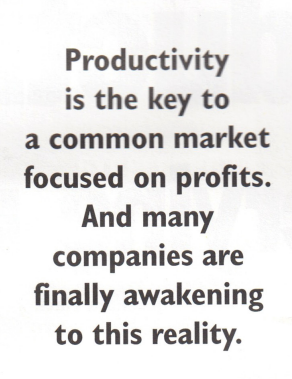
cost/quality leadership.’ The company saw a 25% increase in productivity levels in 1996. ‘We have an educated, understanding labor force who actively participate in all discussions and problem solving. We work together as a team, and we achieve results as a team. We have an open office concept, where directors, executives and members of the staff work at their work-stations andconverse freely and build team understanding,’ said a spokesperson for CTC.
Another company recognized and rewarded for their improvements in productivity was Arpidag International, a joint venture between Richard Pieris & Co Ltd, and Bandang Inc., a Fortune 500 Launching operations in 1991, Arpidag introduced a revolutionary tyre retreading system to the country. Achieving high standards of quality, productivity and technical service were the main focus of the company, and having achieved this remarkable feat, they now focus on maintaining and improving on these standards wherever possible. Customer confidence has been won by the consistent quality of Arpidag tyres, and the company believes that the number of Arpidag tyres in use will grow to approximately 50% of the market share, in 1997.
Productivity is the key to a common market focused on profits. And many companies are finally awakening to this reality. For some it may mean complete re- structuring, for others a change in focus. But whatever it takes, it is certainly time to take the improvement of productivity seriously.