The first consignment of Lux toilet soap – popularly referred to as the beauty soap of international film stars’ and valued at Rs 33 million was exported to Bangladesh recently by Unilever Ceylon.
This shipment was followed by another consignment of 500 metric tons of Lifebuoy soap valued at Rs 25 million.
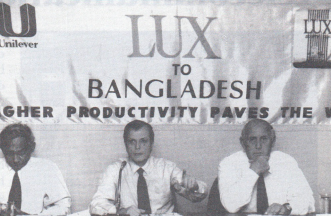
on his left the new Chairman Mike Thompson
The 500 metric tons of Lux is 12 percent of Unilever’s annual production volume and the 500 tons of Lifebuoy 10 percent.
This, apparently, is the first time in 60 years that Unilever has been able to win the Lux export order to Bangladesh.
The Bangladesh High Commission’s Commercial Attache here, Shaiful Islam, vouched for the competitiveness of this product – both in quality and price as compared to that of the other current suppliers.
“We are also negotiating to export other products”, said Unilever’s out-going Chairman, JJ Wolfer, a day prior to his departure from Lanka to take up his new appointment in Hong Kong.
He attributed his company’s export achievement to its endeavour of making maximum use of the available plant and machinery and a change in the working patterns – a system whereby the meal breaks of its workforce were staggered and the production line kept going for 24 hours.
This system was conceived, he said, not only to increase productivity to meet the growing demand for soap, but also to take the maximum benefit from their capital investment of Rs 1,500 million on the buildings and machinery.
With this increase in production, the company saves approximately Rs 150 million per annum.
With this new work pattern, Unilever will be in a position to produce six million more pieces of soap annually.
We used to lose 6,900 tablets of soap at every lunch break of 45 minutes, said Unilever’s Technical Director Dr S AK Abayawardana.
Each metric ton contains 69 cases and each case 100 tablets of soap. This change in the application of different working patterns has also resulted in Unilever having to pay its 1,000 employees attached to the factory in Grandpass, an additional Rs 14 million.
Wolfer made it quite clear that it was the machines that were being worked right through the day and not the employees who still enjoyed their lunch and tea breaks as usual.
He also hoped Unilever would be able to maintain this new system succesfully and achieve the present production quota at least, if not more, not only for the benefit of its employees but also for its customers and shareholders.
Director Personnel, TP Gunawardena attributed their success to employee cooperation.
Although it is possible to use this equipment for 365 days of the year, it was used only for 80 days, said Abayawardana.
Providing a statistical breakdown of the equipment’s working hours, he said people kept away from work for about 40 of the 365 days. There were tea and lunch breaks and at the end of it all what they reaped was a 40 percent production rate of these 365 days.
This productivity increase was achieved not only by a change in the working patterns but also by upgrading the skills, having a monthly skills operation pool to tide over absenteeism, evolving a system of working with the employees in groups, having employees take care of the work share of their colleagues during their absence and also by resorting to TPM (Total Productivity Maintenance), the handing over of the ownership of the production line to the employees whose responsibility it was to maintain it in good order. And more importantly, relying on them to work seven days of the week. A machine must work 168 hours per week, said Abayawardana.
Unilever manufactures 120 different products ranging from soap, toothpaste to food items.
It is a subsidiary of Unilever PLC, the Anglo-Dutch Company. operating in more than 90 countries with over 300,000 employees and an annual turnover of over US $ 49 billion.
Unilever Ceylon, an integral part of the global Unilever family has an annual turnover of Rs 800 million.