When Dr Dan Godamunne fir t submitted the idea of re-manufacturing photocopier parts as both a cost-cutting and environmentallyfriendly mechanism, there was scepticism among his colleagues at Sydneybased Fuji Xerox.
This was in 1993 and although Dr Godamunne was a freshman in the Australian corporate sector, he had a brilliant history of cutting-edge expertise behind him. A physicist, mechanical and electrical engineer, Dr Godamunne had given up impressive engineering postings in the US and UK to test the waters in Australia. And it was this grand track record that convinced his bosses that he should be given the green light to proceed with the idea of breathing life into dead photocopier parts.
His idea paid off and today Fuji Xerox Australia’s Eco-Manufacturing Center (D1C) in Zetland Sydney, headed by Dr Godamunne, employs more than 130 and provides the company a cost benefit of around AUS$25 million per year. Few would have believed that used and worn out parts of a photocopier machine, rather than being treated as waste, could be reengineered, in an eco-friendly manufacturing process, and turned into a better-than-new component. But that’s what was being done, very successfully .at the EMC.
Today, Dr Godamunne’s achievements and the EMC’s success have been well documented in the Australian media. Moreover, his brilliant idea has found a place as a permanent display at the Sydney Power House Museum after the EMC won the prestigious Australian Museum Eureka Prize for Industry in 2002. As a direct result of the EMC’s dedication to environmentally responsible corporate practices, the company was admitted to the United Nation’s Global 500 Environmental Roll of Honor. The company has also won environmental and engineering awards for their approach to eco-manufacturing.
All these feathers sit light on Dr Godamunne’s cap; he remains a simple man and a true Sri Lankan at heart. Hailing from Ampitiya, Kandy, Dan had his early education at Trinity College, Kandy and then moved on to St Benedict’s College, Colombo. In 1972, he left for England to do his A/Levels and thereafter entered the University of London where he received his degree in engineering. He then studied at the prestigious Cranfield Institute of Technology in England where he earned his doctorate. His career history begins with Xerox in the UK, and later US, where for 11 years he worked as part of the Research and Development Division. He has several patents in his name in the area of heat transfer and work on magnets.
In 1989, Dr Godamunne moved to Australia and began work as a project manager for Ford Motor Company. He then moved on to Fuji Xerox Australia.
A committed environmental-ist, Dr Godamunne believes he inherited his love for nature from his father, champion of animal rights and the leading light behind Gal Gawa Mithuro, Dr Cecil Godamunne. Dr Dan Godamunne also says he believes it is the hand of god that supports him in all that he does.
In this interview, Dan Godamunne, General Manager-EMC, Fuji Xerox, Australia, tells us how a seemingly simple idea has had a dramatic and far-reaching impact on his company, the community and Australia as a whole.
By Raine Wickrematunge
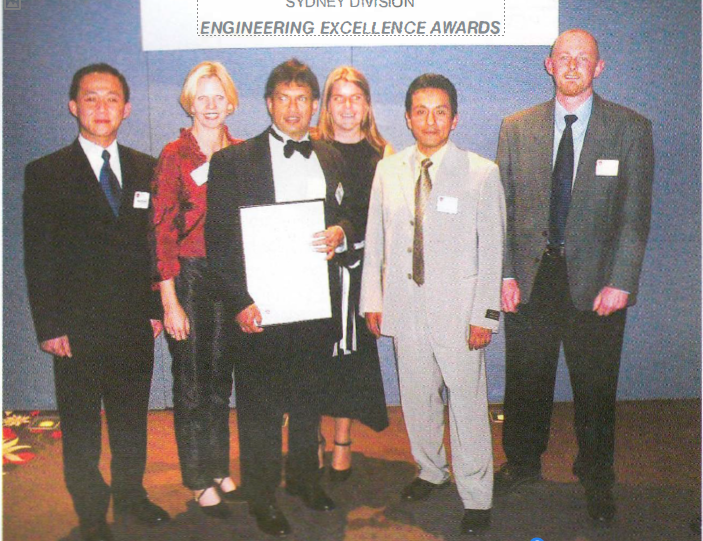
Development Division. He has several patents in his name in the area of heat transfer and work on magnets. In 1989, Dr Godamunne moved to Australia and began work as a project manager for Ford Motor Company. He then moved on to Fuji Xerox Australia. A committed environmental-ist, Dr Godamunne believes he inherited his love for nature from his father, champion of animal rights and the leading light behind Gal Gawa Mithuro, Dr Cecil Godamunne. Dr Dan Godamunne also says he believes it is the hand of god that supports him in all that he does. In this interview, Dan Godamunne, General Manager-EMC, Fuji Xerox, Australia, tells us how a seemingly simple idea has had a dramatic and far-reaching impact on his company, the community and Australia as a whole.
It was all about making the senior management appreciate that there was commercial gain to be made through the venture. I demonstrated a case study related to a toner cartridge I had patented and there was a level of confidence because it had been my original idea. Although there was some apprehension at the beginning, there was also trust and confidence that I would deliver what I promised. My credentials too, I believe, influenced them. At the end of the day, if you can say to ·senior management, “Yes, we can do the recycling and the re-manufacturing in a cost efficient way and all the investment you put in will give a year on year return,” they will listen to you. Since 1993, when we began, our growth has been exponential in every way. Year on year we have grown over 20%. In the first few years of operation, there was still some apprehension at senior management level and investment was low. But with proven results over the years we have not only made it feasible within the Australian operation but a part of the international one. Fuji Xerox now has re-manufacturing factories in nine locations – Europe. North and South America and the Asia Pacific region.
How much convincing did it take to make acceptable the notion that remanufactured products were en:n better than new, among customer and service operators?
Theoretically, it can be proved. You take a product that was designed yesterday and improve on it using today’s technology by studying the inherent problems and re-engineering it to enhance its yield and life. When a product is put to the test in the laboratory, it can be accepted but the acid test is proving its efficacy in the real world. Once we were able to convince customers that what we were doing was exceeding the life expectancy of a product, then they were with us.
People have a perception about recycled products and they use the term ‘second-hand’, which I dislike very much. It is a re-processed part, as good as new. The difference in what we do, compared with the corner shop, is that we test it functionally. Sometimes parts may work at 80% but we will not accept that; we get 100%. We now have customers who ask for the re-processed product, not because of cost, although cost does have a part in it but als0 because of quality.
Today, Dr Godamunne’s achievements and the EMC’s success have been well documented in the Australian media. Moreover, his brilliant idea has found a place as a permanent display at the Sydney Power House Museum after the EMC won the prestigious Australian Museum Eureka Prize for Industry in 2002.
Your personal vision, and now that of Fuji Xerox Eco Manufacturing Centre has been sustaining the environment through better technology. Can you describe how this vision is put into practice in your day-to-day operations?
Basically, we look at all used components as company assets and we utilize that asset by turning it into a better-than-new product. At our EMC, we conduct six operations involving fuser rollers, laser optical systems, electronics, magnetic rollers, mechanical assemblies, and print cartridge re-manufacture. The first – fuser rollers – involves re-coating them to exact specifications that ensure high quality photocopies and longer operational life. The re-manufactured fuser rollers are superior in quality to the originals. Signature analysis, a technology we use in the re-manufacturing process, has helped us to reprocess magnets and this procedure has resulted in saving the company AUS$40 million worldwide. This innovation was a front-runner for the national Eureka Science Awards. Print cartridge re-manufacture was one of the first operations undertaken by the EMC. We now collect 80% of Xerox cartridges – about 11,000 per month – which are re-processed.
Magnet re-processing has also been very successful. It was a fairly simple idea that has paid rich dividends. We found that by introducing a simple coil spring. we put a factor of 2.5 times into the life of the product. The average life of 1he current magnet is 1.2 million prim , but this gives us 3 million prints. I am also part of Xerox technology development council and I get asked to review products for their recyclability at corporate level.
The company has struck a happy marriage between environmental and business interests. How and when did your passion for the environment begin?
Even as a child, I never had any of my toys in one piece. I took them all apart and put them in collection boxes and utilized them in some other way. I guess I was an engineer even then! Much later, when I was working in the US, I was appalled at the volume of industrial waste that was being disposed of into landfill. I considered it to be an asset and we were throwing it away. I developed a passion for industrial waste management.
Still on the environment, could you give us an example, in figures, of a direct benefit to the environment as a result of your work, perhaps with reference to reduced landfill?
Currently, of all used parts that come into the EMC, we send out only 7% to landfill. Our objective is to reduce this figure to zero by 2006 as per our current corporate policy.
An important part of your business strategy would have to be recovering components from customers for remanufacturing. What is your recovery rate and what recovery system do you follow?
Our recovery rate is over 80%, depending on the product. Some are as high as 98%. We use courier services and our service engineers who replace parts at our customer sites to retrieve used item . We have a supply chain management system in place to monitor all re-manufactured parts and return levels down to individual service engineers and couriers.
The EMC is on a constant search for ways to re-use components and materials and has developed around 400 remanufacturing programs. Obviously, even the tiniest of components is not overlooked. For instance, the re-design of a 15 percent spring on magnet rollers Fuji Xerox Australia, AUS 1 million per annum. Your success must induce other companies to approach you for bu in solution for themselves? If yes, could you give u some examples?
We have been closely working with CSIRO (Commonwealth Scientific and Industrial Research Organization) in Melbourne to diversify our business into the automotive industry. Our involvement is still in the proposing and planning stages, and we have a plan to re-manufacture components to be as good as new. We have done case stll(;lies on the gearbox, steering column and auto braking system, and we need funding to develop these into prototypes. Funding for research is very hard to come by so our efforts have not borne fruit a et. One positive thing. however. i that there is legislation currently going through the senate to penalize manufacturers who add to waste. This legislation, which was heavily lobbied by the green parties, will come into effect in 2006. The EMC has also taken the initiative to influence the impact other companies have on the environment through a series of programs. We organize tours at our center to make other companies aware of how and what we do here, and we advise federal and state governments on sustainability and have developed ties with educational institutes.
Another principle of Fuji Xerox is ‘Waste free products from waste free factories’. What steps do you take to reduce or eliminate the emi ion of harmful pollutants and waste during the re-manufacturing processes?
Basically, all emissions are filtered and tested by the Environmental Protection Authority. Even the water is re-cycled and re-processed. Nothing ends up in waste. All technical processes at the center have been designed to eliminate environmentally damaging emissions. We ensure that all solvents have been removed from the cleaning parts and components, dry ice or frozen carbon dioxide is used under high pressure to clean components, environmentally neutral bicarbonate of soda is used under high pressure to remove the original coating from fuser rollers, and all metal parts that cannot be used are sent for recycling. We are also conducting research into ways of minimizing packaging waste including plastics.
Before the birth of the EMC, almost 100% of Fuji Xerox product parts were imported into Australia. Today, 74% of all parts by value are re-manufactured at the center. Your aim is to be able to re-manufacture 100% of all parts. How are you working towards that goal?
Our aim is around 80% and we are well on track.
As a result of cost saving, Fuji Xerox has benefited enormously. Your customers have benefited through reduced running and disposal costs. The community has benefited through reduced landfills and increased employment, and the country has benefited through reduced imports and limited pollution. Thus, you have achieved a great deal for yourself, your company, your customers and your adopted country, Australia. Do you have a vision for Sri Lanka, in an environmental sense?
You missed another benefit – reutilizing base material which helps the earth’s resources. As for Sri Lanka, it is my country of birth and I wish it everything that’s best. I hope that a similar process to what we are doing here in Australia can be utilized in countries like Sri Lanka which would have more to gain through such a system. It certainly has the capacity, and eliminating and utilizing waste will be so beneficial to growing its industry and economy. We are blessed to have been born into such a beautiful country which has so many of nature’s wonders thus we need to preserve it.