Sustained Productivity and Quality Improvements
Falk O Petersdorf and Joachim Leckscheidt Sri Lanka – German Private Sector Program
The expression of content in the face of the ambitious Sri Lankan entrepreneur did not last very long. After having successfully implemented some measures for productivity improvement, he realized: ‘this is not enough for the future, what we need is to change the company culture.”
This impression of a great need for improvement in productivity and quality is largely backed by a survey commissioned to Lanka Market Research Bureau Ltd., by the Sri Lanka-German Private Sector Program (PSP). Out of 70 from the most advanced export-oriented companies in Sri Lanka, only 21% were satisfied with their current productivity and quality level. The large majority sees enormous potential in this area.
Yet, most managers today still understand the challenge of productivity and quality improvement in a rather traditional way. As the same study shows, the majority of improvement measures introduced by these companies concern isolated techniques, such as improved machinery, increased capacity utilization, reduction of waste, or materials handling. Traditional approaches to productivity and quality improvement are most often one-dimensional and technical.. A knowledgeable engineer improves the output of a crucial machine, rearranges the workshop, or introduces new technology. Granted, these activities do deliver an immediate jump in productivity but this is only a one-time gain. Intensive discussions with Sri Lankan executives showed that the really progressive minds were not happy with these one-hit techniques and opted for the long-reaching approach of changing the entire company culture.
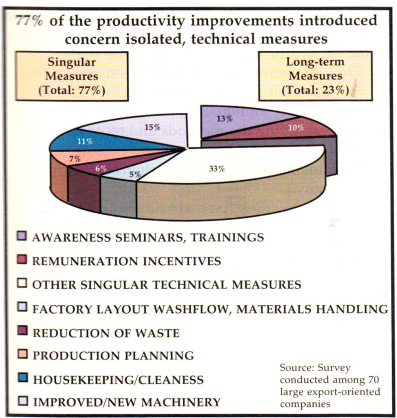
Success stories around the world confirm that the most effective method for long-term productivity and quality improvements is a companywide cultural change. This means to redirect the organizational behavior and implant motivation and capability in every single employee to discover ways to improve productivity and quality in his/her workplace. Who knows more about the tools, the machines, and all the little things that can go wrong than the staff that has its five senses on it every day. Not even the most educated technical specialist can reach up to the combined knowledge of the employees regarding the company’s work processes. Making use of this potential for continuous improvement must be the objective of a companywide cultural change. In Europe and the USA, even successful enterprises have been striving for years to get there. Sri Lanka, with its agonizing polarization between management and workforce has a long way to go.
On first sight, the concept of company culture seems very intangible and difficult to grasp. Yet, attitude and behavior of employees regarding productivity and quality largely depend on it. The culture of a company concerns the whole environment in which the employees fulfill their duties. Some important elements of company culture are:
Management style
- Strictly hierarchical vs. delegating decisions to lower levels
- Goal setting and clearness of expectations
- Constructive feedback or punishment
- Entrepreneurial thinking and initiative-taking of middle management
Set of rules and guidelines
- Company policies.
- Job Descriptions
- Quality Systems
Incentive system
- Basis for payment: working hours, quantity, quality
- Premium or reward system for excellency
- Job security and loyalty of employees
Communication
- General openness in communication: Do people say what they think?
- Only hierarchical vs. cross-company independent of level
- Degree of formality of communication: written, oral, fixed forms
Attitude towards progress and innovation
- Openness of management and workers towards new ideas
- Training and educational measures for employees
- Knowledge of customer requirements throughout the organization
The above elements can serve as a checklist to analyze and understand the different facets of a company-specific culture.
Understanding the far-reaching meaning of company culture, the entrepreneur is faced with the challenge of introducing a new corporate culture in a way so as to foster every employee’s contribution to the continuous improvement of the two key success factors-productivity and quality. Of all the possible effects of this change, three tools referring to the above-mentioned elements shall be presented to show how the right company culture lays the ground for long-term and sustaining productivity and quality improvements:
The introduction of formal quality systems (like ISO 9000) increases quality awareness and implementation by visualizing the process, stating clear requirements and job descriptions for each work unit. For each working step a clear standard of performance is defined, which should be set at a high but realizable level. Therefore, each employee knows what is expected of him regarding quality and quantity of his output. Expectations, performance and deviation through failures are measured and documented clearly. The performance of the individual becomes highly transparent. Yet, the traditional working environment in a typical Sri Lankan company is still rather punitive with a prevailing motto: ‘Don’t stick out your neck!
Basis for forming a productivity and quality-oriented company culture is to build competencies among workers and particularly among management. This requires a formalized training program. Workers need to be made aware of the necessity of continuous improvement in the workplace and be given simple but effective tools to implement them. Middle management plays a key role in guiding the improvement process. and being a good example. Therefore, their training should focus on leadership issues and communication techniques. If management cannot facilitate an open communication atmosphere, the best ideas of their staff will stay in some hidden corner of their heads. Clear goal-setting for the staff, constructive feedback without punishment and tearing down traditional hierarchy barriers are typical issues to be tackled in this context of cultural change.
Motivation is basic to all human behavior. In a working environment employees will eventually be motivated in the long run only if they end up with money in their pocket. A performance-oriented company culture applying effective incentive systems therefore is a key factor to promote continuous productivity improvements. This generally does not pose a problem to the entrepreneur since every productivity improvement also means direct money in the pocket of the company. There are many forms of effective incentives: Performance-oriented wage systems based on the quantity and quality of the work are only the beginning. A transparent and honest reward system for suggestions and initiatives to increase productivity is bound to attract the attention of each worker. Many Sri Lankan companies have experimented with various incentive systems. Handicaps regarding productivity improvements arise from the fact that only a few companies have their standard time and performance criteria well in place to make individual success visible.
Practical experience has shown that the positive effects of cultural change go far beyond what is mentioned. As opposed to singularly technical improvements due to a new machine or a one-time rearrangement of the workflow, cultural change will ensure the continuous improvement to the various aspects of productivity and quality through the contribution of the whole workforce.
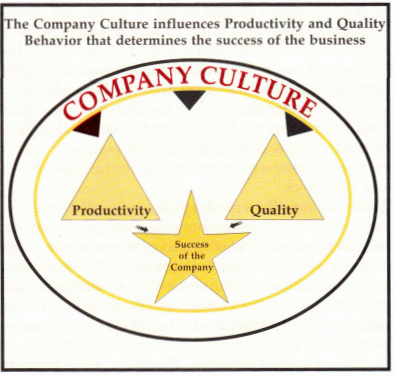
Although most effective for a long-term improvement in productivity and quality, a companywide cultural change process is not easy to implement. The focus has to be upon building the productivity and quality-related competencies among the employees as well as designing adequate motivational programs. Basically, this process comprises three steps:
(1) Creating awareness and motivation among the management and the workforce for matters of productivity and quality;
(2) Understanding the methods and tools for productivity and quality improvement;
(3) Implementing the tools and changes within the company.
Many companies have already started with this process, some have accomplished great steps already. The results of the above-mentioned survey also show that some Sri Lankan companies have already adopted certain methods and techniques for change. Along with improving the technological side, cultural aspects like motivation, guidelines and training are becoming more popular.
Singular but impressive results through cultural change can be observed in all industries. After conducting productivity and quality seminars combined with a new incentive system, the employees of a Sri Lankan toy manufacturer, for example, now produce 40 suggestions for improvement per month on average. They have institutionalized quality circles, which have brought about dozens of measurable productivity improvements. One, for example, was to reduce the costs of a key product by almost 20% within 6 months.
Fortunately, the Sri Lankan economic environment offers a wide range of Service Institutions, which help entrepreneurs to start the cultural change process to- wards a productivity and quality-minded workforce. ‘Productivity Cells’ have been formed under the Ministry of Industrial Development and the Federation of Chambers of Commerce and Industry of Sri Lanka (FCCISL), which have successfully carried out seminars and training in productivity awareness, concepts, and implementation. On top of that, there are a range of other governmental and private institutions which are ready to guide Sri Lankan companies into a long- term sustainable productivity improvement process through cultural change.
Sri Lanka finds itself in the beginning of the decade of productivity. A decade in which the country’s economy has the chance to lay the fertile grounds for success and strengthen its position as a recognized producer in a competitive global market. However, entrepreneurs should not just be satisfied with short-term improvements in their production process but light the spark towards a truly productive and quality-oriented company culture.
Falk O Petersdorf is an economist with several years of international experience in Management Consulting and Training and works as Productivity and Quality consultant. Joachim Leckscheidt is head of Project at the Sri Lanka-German Private Sector Program(PSP), a project of the Ministry of Industrial Development, Sri Lanka and the GTZ-German Development Corporation.