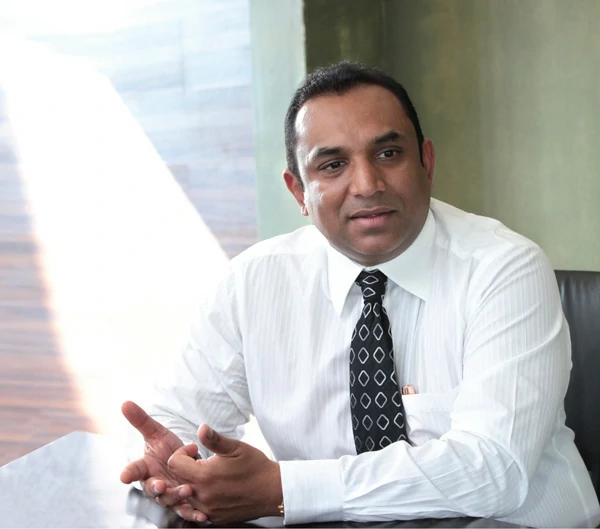
Lakshman De Fonseka, Managing Director of JF Packaging has excelled in taking his father’s company to great heights, making it one of the leading local packaging suppliers with a reputed clientele. The strength behind the company’s latest state-of-the-art manufacturing plant, De Fonseka speaks about his aspirations for the future of the company and the endless potential for Sri Lanka to promote the industry.
By Kamalika Jayathilaka
Photography Prabath Chathuranga
JF Packaging is a pioneering manufacturer and supplier of a wide range of packaging solutions to reputed clients both locally and internationally. As the Managing Director how would you comment on the company’s journey so far?
My father Joseph De Fonseka, established the company in 1987 in Pallekale, Kandy, in an industrial estate. He started the business with LDP material (low density polyethylene packaging), or in general terms Polythene. Even though he was from Colombo he established the factory in Kandy at the request of a parliamentarian, not with the hope of earning profits, but with the intention of helping the people of that electorate through the creation of employment.
In the meantime, I was studying in Australia. Soon after returning to Sri Lanka, my father asked me to work for his company; and I started working for him initially for Rs 750 a month. At the time I started working, the company was at its initial stages, and as such it failed to interest me. I wanted to do something more, to develop and improve. Therefore, I initiated its lamination section after moving to Ja-Ela.
It was in 1995 that we began the plant in Ja Ela; we were the third company in Sri Lanka to venture into this industry. But, this was a very challenging time and on the day we were to open the plant there was a terrorist attack on the Central Bank. We had large scale dismantled machines and needed the expertise of engineers, but because of the situation at the time they were unable to come. As a result the entire project got delayed by one and a half years. This is one of the major challenges that we faced. There were other challenges that we managed to overcome and in 1996 we were the first to introduce multi layer co-extrusion in Sri Lanka. We were also the first company to introduce barrier films. Likewise, we have always been forward thinking, wanting to be one step ahead in the industry. This year we went through further expansions and invested above 450 million rupees mainly because we felt that this industry is growing at about 15 percent per annum and the living standards of the people have significantly increased. Most consumers today prefer to buy packeted or packaged goods. Therefore, we felt that it was the most appropriate time for an investment of this magnitude. Our latest plant which we initiated about six months back is on par with any European factory in terms of equipment and technology. We have achieved so much since our inception and today, we work with all the leading companies in Sri Lanka.
With regards to staff we currently have over 100 employees, and some have been working for me for over 15 years since the inception of the Ja-Ela plant. There are those who have come from the Kandy factory to Colombo. Our Director Marketing has been with us for over 25 years and is the oldest in the company. We do not have any unions because we take care of our people very well; we are like a family.
I believe that the greatest strength of a company is to be able to retain the staff. If there is a turnover, if people change constantly there is no sense of stability. That is a key factor for us to achieve what we have achieved today. I respect the human ability, and uphold human resources as significant. Your strength is not in your machines, technology and equipment but your staff. Therefore, you need to have brilliant human resources in your company.
Our Latest Plant Is On Par With Any European Factory In Terms Of Equipment And Technology.
The company is an industrial leader in flexible packaging mainly serving the food, garments and medicinal industries and is today ISO 22000: 2005, ISO 9001:2008 and HACCP certified. What does this signify for a packaging company?
Keeping our vision, mission, quality policy and quality assurance in mind, we design our packaging to suit the product requirements, presentation, food and safety requirements according to the customer needs both locally and internationally. The flexible packaging materials for food are manufactured according to the HACCP standards. All this is done in the most cost effective manner but, never compromising on quality as we always believe that, our customers deserve the best.
The ISO standards are basically about maintaining a set of documents. The HACCP on the other hand is a very strong, calculated and serious quality control method. Any industry involved in the manufacturing of food must hold a HACCP certificate. Though we are not a food manufacturing company, most of our packing material is for food. Therefore, we felt that it is best that we too follow the same stringent quality methods and procedures in order to be a quality supplier to our clients. For instance Nestle maintains very high NQS (Nestle Quality Standards) in all their pre and post production processes and if we make a mistake from our side then their efforts will be of no avail. Therefore, we make every effort to instill and maintain the same level of hygienic conditions in our plant.
Initially, Unilever and Nestle Sri Lanka imported all their packaging materials but later decided to purchase from the local market. We became one of their suppliers. Last year and the year before in the audit conducted by Unilever Sri Lanka, we were able to score 100 marks, a full score, because they were very happy with our supplies, the hygienic conditions in the factory and the way we were working with them. As a result we earned the A-Rated Quality Supplier of Unilever Sri Lanka Award for the quality and delivery of our products and services. Unilever Sri Lanka treats us as their business partner. Our chemistry works very well. As a result we are working with them on a very large scale. They are one of the best companies to work with and they understand how to maintain supplier relationships. We have a very good relationship with them.
Could you speak a little about JF Barrier Films as a new addition to the JF Group?
JF Barrier Films is a new company that we began about one year ago. We made an investment in a high-end multi layer film plant with six metric tons of capacity per day. The main scope of the venture and the reason behind it, is the difficulty in the purchasing of raw materials. Sometimes with certain suppliers there is a requirement to buy fixed amounts of material even beyond your need. Investing on unnecessary supplies is an added cost, and it is a problem faced by many Sri Lankan packaging companies. There is scope for the Sri Lankan laminating and packaging industry to grow. JF Barriers has the capacity to supply raw materials to all the other companies like ours so that they can concentrate more on their core business and buy the raw material from us. We developed JF Barriers on that basis. Currently, we provide a multi layer film but we are hoping to institute a CPP (Cast Polypropylene) plant and then in another few years perhaps a metalizing plant as well, concentrating mainly on manufacturing different films.
In other countries companies do not do everything in-house. They give sub contracts in order to give full concentration to their core businesses. But in Sri Lanka for some reason when starting manufacturing plants they want to install all the machinery and sometimes they don’t have enough working capital to support this. I had this in mind when we opened the new plant; our aim is to help the industry as it needs to grow.
JF Barrier films has a vision to become the most reliable barrier films manufacturer to the flexible packaging industry and envisions to issue IPO within the next two years. Can you elaborate on this?
Growth is essential for any company. In the same way JF Packaging perhaps at the end of this month would be able to go for a private placement. We will be issuing about 30 percent of the company to the public, because what I feel is that in Sri Lanka entrepreneurs try to keep companies to themselves without allowing others to join them. When a company reaches a particular level of business turnover you should get other professionals and experts involved in the business in order to expand the business and let it grow. Therefore, if you want to export and expand, you need new capital coming in. Professionals coming into the company will be a stepping stone for the company’s growth. This is why we are moving to be a public company.
With globalisation and internationalisation, the world garment industry has undergone production migrations to Asia and the developing regions with increased potential for the packaging industry. How would you comment on this and what implications would this have for the packaging industry in Sri Lanka?
It was about 30 years ago that the garment industry started migrating from Europe and USA to Asian countries, mainly India, China, Indonesia and Korea. After 1977 the industry began in Sri Lanka. The support of the Government created massive market potential in the country in the 1990s. Currently, the same phenomenon can be perceived in the packaging industry. The European and American markets are not willing to manufacture packaging materials any longer and are mainly purchasing from countries such as China and India. This is a significant opportunity for Sri Lanka. The infrastructure facilities in the country have been greatly developed, Sri Lanka has one of the best banking systems in the developing region with minimal red tape. Therefore, if we try to capture these markets this will be a profitable industry for Sri Lanka for another 50 to 60 years. Packaging is a large-scale industry. Currently, the major players are India, China and Indonesia. Even though we currently export to Maldives and the African countries, we have yet to enter the mainstream of clientele.
If you take the plants in India, they are producing over 1,000-2,000 metric tons, but at this plant we produce only around 200 metric tons. There is a very large gap. Therefore, it will be challenging. The machinery required for the garment industry is not very expensive, it mainly relies on man-power. On the contrary, establishing a packaging plant is rather costly as the machinery is very expensive. We need at least USD five to six million for equipment alone. However in this plant we need less man-power. If the Government can offer the same support that they give to the garment industry, Sri Lanka has a massive potential in this industry.
If We Try To Capture These Markets This Will Be A Profitable Industry For Sri Lanka For Another 50 To 60 Years.
The company embarked on its most ambitious expansion project to date with the opening of the company’s state-of-the-art European machine equipped factory. Could you speak about its significance?
We have expanded our services to match the increased demand for our products. The cost of the total investment consisting of machinery, land development and factory building amounts to USD 4.5 million. With this new investment, our total installed capacity has been increased up to 300 percent. Higher proportion of the investment is in the machinery that is environment-friendly, cost-effective and consists of the latest technologies. The countries of origin of the machinery are Europe, Taiwan and India. Specifically, the multilayer can extrude at a minimum of 18 microns. None of the other extruders in Sri Lanka could reach such a low gauge. It is able to produce film to cater to any industry. We also have a laminator, which is the first of its kind in Sri Lanka with 11 technologies in one machine. It has a drying tunnel with high efficiency drying capacity. It’s a high speed machine that runs 400m per minute.
However, we hope to expand into a new line within the next year to further increase our capacity. We are currently running only two shifts. The plant is closed from ten in the night to six in the morning.
Could you elaborate on JF Packaging’s efforts to remain abreast with latest technology in the world?
There are a number of major international exhibitions in countries such as Germany, India and China. We make sure that we send our team to represent the company and we also make sure our employees get an opportunity to attend international seminars and workshops so that they can see what is happening around the world. We develop our technology and move forward based on the knowledge that they bring back. We also invest heavily in our machinery and equipment. Most packaging companies in Sri Lanka will invest largely on printers but not on laminators; but we purchased our laminator from the world’s best laminating machinery manufacturer, and selected one of the most high-end equipment in their product line. Even in India they have sold only a few of these machines. However, we made the right decision and as a result we have the potential to move into the international market. This is a significant move because if we want to cater to an international clientele they will want to know the type of equipment we use; because with the list of equipment they determine whether you are capable of supplying to meet their needs.
Apart from that we have also invested on a high-end eight colour Gravure printer. This machine is suitable for multi-colour computerised continuous printing. It is capable of high speed and quality, printing with maximum printing capacity up to eight colours. This also has a printing tolerance of 50 microns whereas, the average printing tolerance of Chinese/Taiwanese printers are over 100 microns. As a result we can print any design that a client requires. Therefore, it is a continuous process to keep in touch with what is happening around the world in terms of technology. Packaging is similar to the IT industry. If you are not in step with the technological advancements you will fade away in a few years.
Could you explain the significance of environment-friendly manufacturing and the company’s current efforts and future plans in contributing towards greening product activities?
Considering our old factory, it is 14 years old and uses relatively old technology. Therefore, certain environmental aspects were overlooked. From the point of designing the new plant however, I gave priority to the environment. Usually when setting up manufacturing plants in Sri Lanka they make a shed, include all the machines inside and cover it completely, provide electricity to the plant and try to run it. I don’t believe that this is the right procedure. When a technician works at a machine he should have an appropriate mental condition. He should not be stressed out. If you visit our factory floor you will notice that the entire factory is covered in glass; and the factory overlooks the surrounding marshes with views of the beautiful scenery with the birds and the greenery. This serves as a tremendous stress relief for the people.
On the other hand the machines we use create less wastage. They are accurate, and as such there is limited wastage. Also, we do not use electricity for heating. We use a boiler, a thermic fluid. This way we reduce the cost plus it is environmentally friendly. We use blowers to take the heat away. We reuse this heat, saving the energy to reheat the next circle of air that enters the plant. These are some of the latest efforts we have made to reduce the cost of energy, which in turn will have a positive impact on the environment.
If You Are Not In Step With The Technological Advancements You Will Fade Away In A Few Years.
Sri Lanka has now emerged as a peaceful country in the region and is stepping into a new era of socio-economic development. In this light, what future plans do you have for the future of the company?
Primarily we hope to venture into the international market and become a very good supplier. Currently, Nestle and Unilver are our main clients and by supplying to them we are working with multinationals. We supply to Prima and Keells. Even though multinational companies are often misunderstood to be exploitative we have come a long way because of some of these multinationals like Nestle, Unilever and Prima, who have come forward to provide us with the know-how when required. They have helped the local packaging industry to grow and reach new heights.
Likewise, we work with a very high-end clientele and want to expand on who we serve. We want to add high barrier film manufacturing plants as well as a CPP plant while importing a vacuum metalizing plant to manufacture metalized foil used for packing tea. Currently, it is not being manufactured in the country; we import the film and do the printing and supply to the customer. This will however be a large scale investment. Having regained peace in the country, infrastructure is being developed; supermarkets are being opened around the country including the North and the East; more and more people use supermarkets, their buying power has increased. This means that more people are getting used to packeted food. A few years back people used to buy shampoo in bottles but today they prefer to buy sachets. As a result the packaging industry will expand.
Thus, the Government should assist this industry as well. This is another industry with potential similar to the garment industry. If you consider the consumer products of the day from food to personal hygienic products, practically everything is packaged in laminated films. Likewise, everything ultimately gets connected with this industry. Therefore, the Government should help develop this industry. If so we can make this a very lucrative industry that would bring capital into the country.
The North and East is rapidly developing. Galle can be reached from Colombo within about 45 minutes which is impressive. If this was developed ten years back our country could have come a long way. In that sense, I am extremely grateful to the current Government for these infrastructure development projects. The time we waste on the road will be greatly reduced. Similarly if we can connect Jaffna-Colombo as well as Kandy-Colombo in similar lines, it will also connect people and solve some of the social issues while providing the opportunity to travel to and from Colombo to every other area in the country in a few hours, then we will experience a major difference.
Research and Development is vital in providing unrivaled packaging intelligence to corporate clients. Could you elaborate on JF Packaging’s efforts in product development and research?
Our strength lies in our in-house product development specialists who are ready to work in partnership with our clients to create high quality products that fully optimise their resources and give them better financial returns. We have a skilled, qualified and well experienced staff to run and maintain our machines according to specific requirements given by the clients. The new product development department is ready to work hand in hand with clients to create their required product. Earlier Sri Lanka was only able to produce PE Films with a minimum thickness of 25 to 30 microns, but with our new co-extruder plant we are able to reduce it to 18 microns. This is a major saving on the cost as well.
We have to understand the ability of our people; whatever the machines or technology, Sri Lankan people are extremely capable. In Europe and the West you need to be engineers to work with some of these machines; but in Sri Lanka these machines are being run by people who are only A/L qualified. Our people are very capable. They can be trained to be extremely brilliant people. If they are faced with a question or a problem they will somehow arrive at a solution. In economic terms this industry is currently very small in Sri Lanka. We have only about five or six plants; but to cater to the Sri Lankan needs perhaps we need at least another ten or 12 plants.
In today’s competitive marketing environment, packaging is what differentiates the product and draws the consumer’s attention; packaging has become as important as the product itself. As a veteran in the packaging industry how would you comment on the development of the industry in Sri Lanka?
What I feel is that more support services have to come into the industry. For instance we need better ink and adhesive manufacturing plants in Sri Lanka. We currently have only about two manufacturers. This will in turn help to develop the industry. A Chinese company has invested in a cylinder manufacturing plant, solving one of the major issues we had. Then, there are other ways of supporting the local packaging industry. When I asked Unilever why they decided to buy from the local market they gave me a very interesting answer. They said that they sell to the local consumer and that particular consumer could be an employee working in your factory and if we don’t help the local industry the local consumer won’t develop and in turn won’t earn enough to buy our products. The same thinking is behind Nestle and Prima. Considering the volumes these companies have, they can easily buy their packaging material cheaper from countries like India. Therefore, they buy from us to help develop the local industry. Recently Ceylon Biscuits has taken a very brave and correct policy decision to buy most of their packaging materials from local companies.
There are many other companies who think on similar lines. Sri Lanka needs about 700 million rupees worth of packaging materials a month. Local suppliers are only capable of providing 350 to 400 million rupees, the balance is imported. The local industry should develop to cater to the full demand. This is the very reason we enhanced our capacities. The industry will be one step closer to that goal whenever a major player like Ceylon Biscuits takes a decision to buy from the local market. Hopefully, this trend will trickle down to other companies; and it will also be an effective advertising tool. As a result both parties will gain.
Developing the industry is not that easy. For instance, equipment used for packaging is very costly. Therefore, the Government should provide more support for those in the industry such as credit schemes and tax holidays. Sri Lanka can develop the packaging industry in the same way the garment industry was developed. This can in turn create a large number of employment opportunities just as in the case of the garment industry. If you consider my staff, up to the junior level executives, all of them are graduates. The others are A/L qualified. Thus, we have addressed two issues; firstly, to provide employment opportunities to the educated youth who pass out from universities and secondly those who have not qualified to enter universities.
Whatever The Machines Or Technology, Sri Lankan People Are Extremely Capable.
Likewise the Government should understand the potential of this flexible packaging industry and if they help us with tax holidays and with low interest facilities this industry will undoubtedly develop to be an enormous strength to our economy.
Any final thoughts?
I wish to show my appreciation to our clients who have supported us a great deal and have been with us for years; companies such as Nestle, Unilevers, Prima and Keells. Keells was my very first client. In terms of financial services, Bank of Ceylon, as a Government bank, has always supported us with their efficient services.
Sri Lanka Can Develop The Packaging Industry In The Same Way That The Garment Industry Was Developed.
Of course I need to thank my father Joseph De Fonseka. He is the person who started the company as a service to the people in Pallekele. My father has only visited this plant twice, for the opening ceremony and on the day he introduced me to the staff. Since then the company has come a long way, a journey of success.
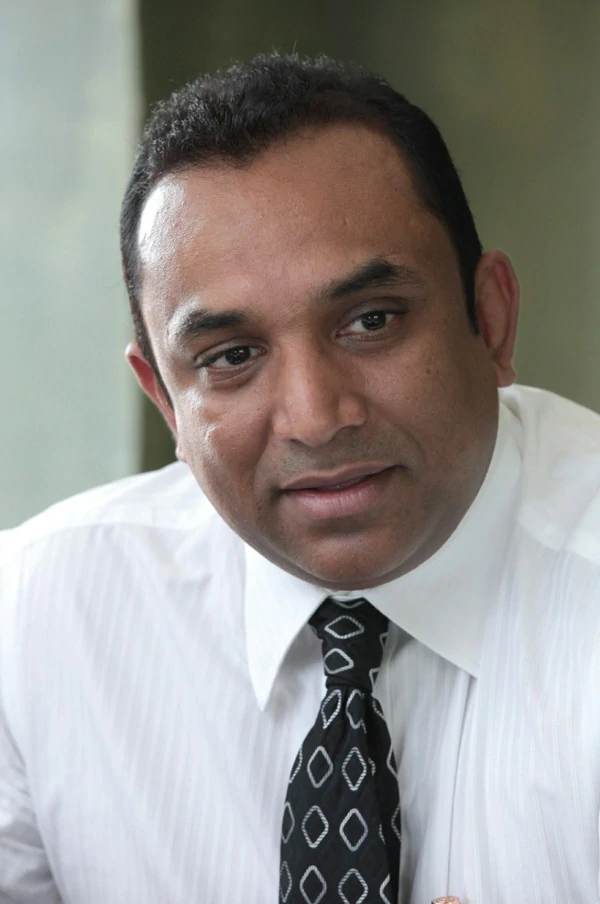
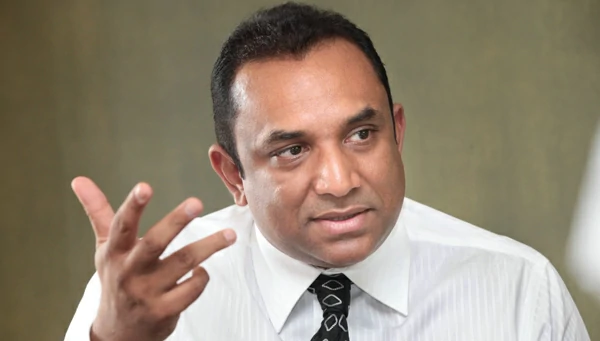
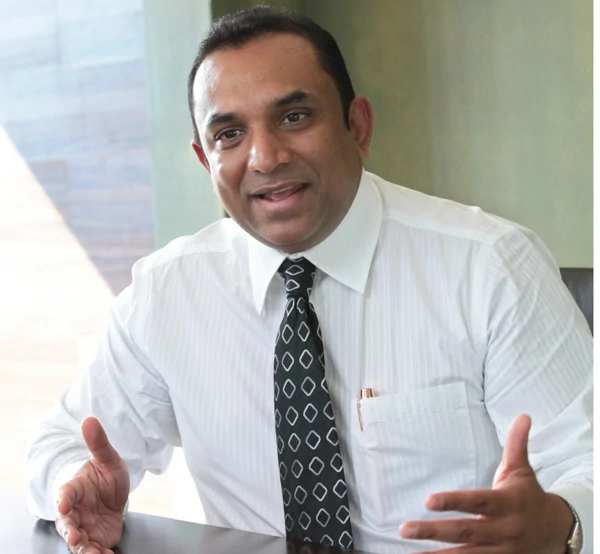